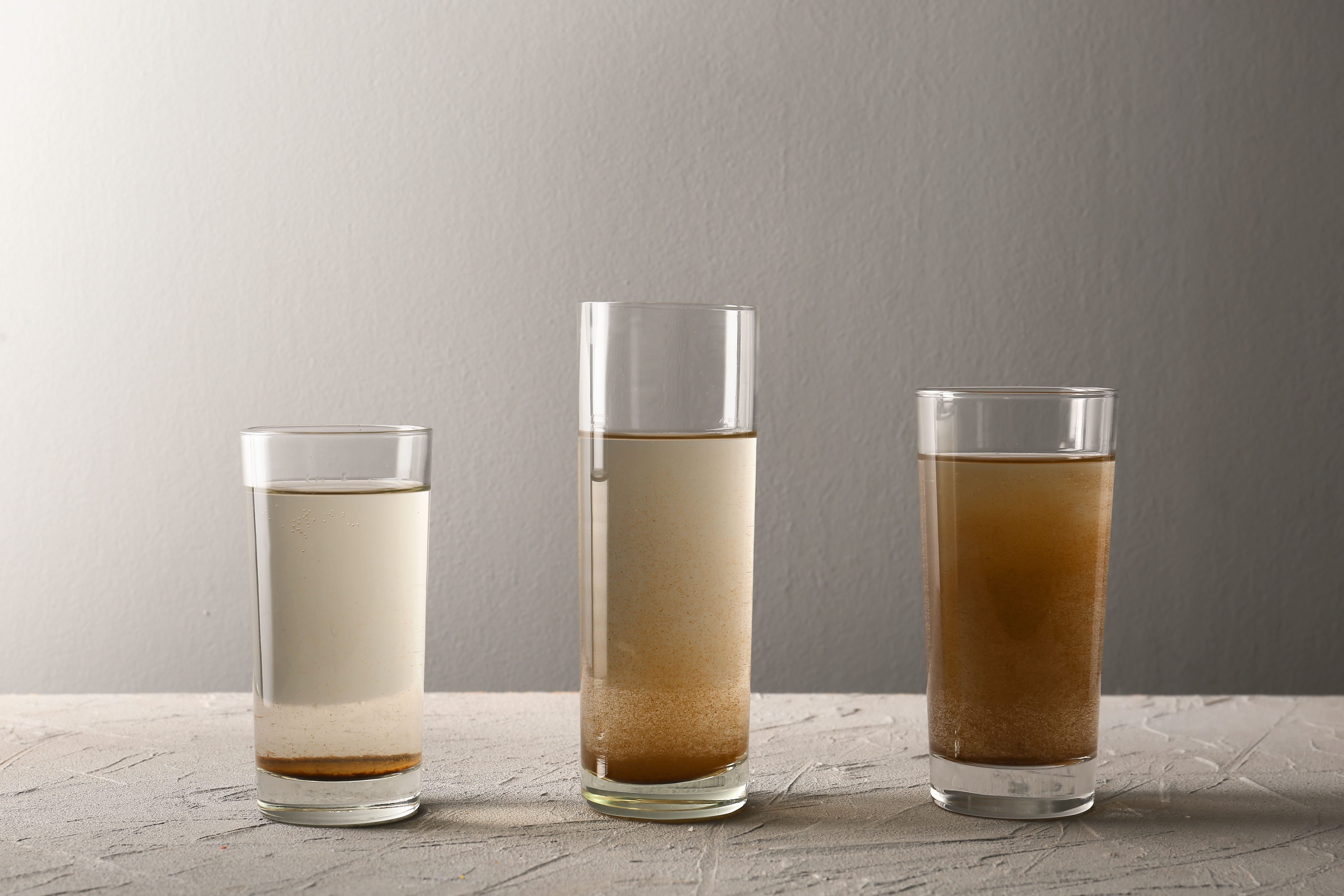
How Contaminant Characteristics and Filter Media Affect Filter Performance
Reduce product waste by analyzing your contaminant’s characteristics and selecting a proper filter media.
Article written by FCX Performance, Inc
We are nearing the end of our Filter Performance 101 series. Remember, it is essential to make sure that your filter is performing at its best so it can extend the life of your downstream process equipment, provide consistent product quality and reduce product loss.
Here are some ways the nature of the contaminant and the filter media can impact your filter’s efficiency:
Contaminant Characteristics
Why is analyzing my contaminant’s characteristics important?
You might be using the filter media that’s inefficient for the application if you are not determining the type of characteristics your contaminants have. This could result in contaminated particles passing through the media or the filter media being plugged prematurely, creating unreasonably short run times between filter changes. Both scenarios can decrease the quality of the product and add additional maintenance costs for changing out the filter.
How can I fix issues regarding my contaminant’s characteristics?
Consider using a graded density filter to tackle many different characteristics of the contaminant. Since this type of media has several layers with varying openings (larger to smaller in the direction of flow), it can trap a range of contaminant sizes throughout its depth while still providing a large open area. This can help extend run times and prevent premature plugging. Similarly, multiple filter media types can be installed in series and address a different type of contaminant or different micron range
Filter Media
The filter media is the heart and soul of a filter system; it has the responsibility of physically removing unwanted contaminants from the process stream. There are a variety of filter media types (woven, nonwoven, metallic, surface, depth, etc.) as well as many different material options, all of which need to be assessed to ensure an optimized solution for the application. Chemical compatibility, temperature resistance and viscosity are also critical factors in determining the most suitable media for the task. The micron size and removal efficiency of the filter media is also essential to consider when selecting your filter media.
Why is analyzing my filter media’s micron important?
A filtration system utilizing a media with a micron rating that is unnecessarily tight can increase high clean differential pressure and can lead to a premature filter replacement. This situation is not ideal due to the high cost for low micron medias. If the micron rating for the filter media is too tight, the media can filter out wanted material or strip away the quality attributes of the product. A filtration system using a media with too high of a micron rating can allow unwanted contaminants and large particles to go downstream, potentially leading to unusable product or premature maintenance of downstream process equipment.
What can happen if my filter media has too much surface area?
The main risk to look out for on oversizing a filter system is to make sure it doesn’t cause issues for batch type applications where the overall volume of the filter vessel needs to be optimized to minimize any product waste or disposal after a batch change. As discussed in our blog about flow rate and flux rate, more filter media surface area leads to a lower flux rate; this always improves the performance characteristics of the filter media. The leftover product in the vessel needs to be disposed or reprocessed, which can become even more critical on hazardous applications.
Filters are a vital part of your plant operation; therefore, it is imperative that they are performing as efficiently and effectively as possible. Stay tuned next month for the last part of our Filter Performance 101 series by following us on LinkedIn.
Talk with an ExpertNeed a better solution to your filtration system? Trust our experts to get the job done with their over 100 years of combined experience.
|